

Are motors with a turn-turn short able to perform continued function?.After failing an impulse test, are motor with weak insulation able to operate?.
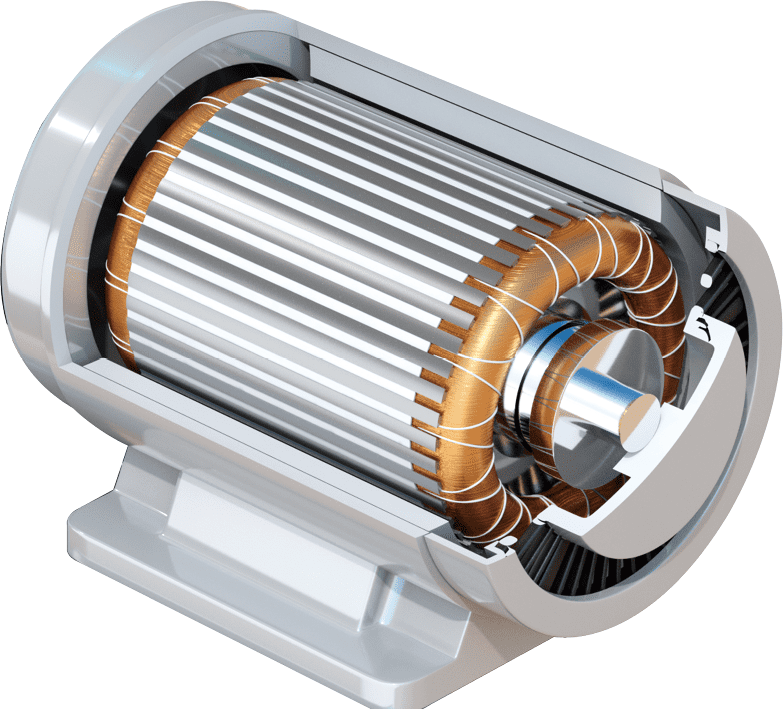
Can DC Resistance, Inductance, Megger or HiPot tests diagnose weak turn-to-turn insulation?.Can impulse testing damage healthy or deteriorated insulation?.Below are few questions that helps in explaining the influence of extensive impulse testing on a motor. They are:Įlectric Motor impulse testing is an integral part of predictive maintenance of electrical motors. What is Done During Electric Motor Testing? There are various kinds of testing done on motor. Some of the winding faults are:įault finding of at least one of the above can save your facility countless hours of shut down and numerous dollars in savings. This creates extra stress and increase in temperature across the fault, which increases until the winding fails. They start as energy crossing an insulation fault like moisture, which sets apart at least one turn. Winding defects occurs due to contamination, ageing of insulation, thermal overload, power surges, damaged wire/materials, and other causes. Many diagnostic tools, such as clamp-on ammeters, temperature sensors, a Megger or oscilloscope, can help illuminate these issues. The other 52% of failures are mechanical faults. The 48% can be again divided into rotor problems (12%) and winding problems (36%). The Electric Power Research Institute (EPRI) conducted a survey which brought into the light that, 48% of motor failures are because of electrical failures. Why is Electric Motor Testing Done?Īfter bearing failure, electrical faults are the most common mode of motor failure, so in addition, a properly planned electrical testing scheme is important for making sure of the plant reliability. But smart companies, understands that without proper maintenance programs, there is billions of dollars of lost revenue through increased motor repair costs, downtime, and waste in industrial and commercial companies. Electric Motor Testing is usually the first thing to be sacrificed when cutting back on operational expenses.

Figure 3 shows the connections for the different leads.Electrical maintenance programs are designed to increase equipment promptness and uptime while decreasing capital operating cost. Their purpose is to provide dual-voltage operation in applications in which the voltage ratio is 2:1. Nine-lead motors may be connected as Wye or Delta, but that decision is made by the manufacturers.
What is a motor winding full#
Centrifugal pumps and fans can often reach full speed before switching to the Delta run mode. Starting torque is also reduced substantially, so the speed at which the transition from Wye to Delta occurs will depend on the inertia of the load. The lower starting voltage reduces the starting current to about 1/3 of normal. This application uses a special starter to Wye connect the windings during starting and shift them to Delta after the motor reaches a particular speed. and Europe, is a low-voltage starting technique known as Wye start/Delta run. Since the impedance of the Wye connection is three times that of the Delta connection, high voltage is connected Wye and low voltage is connected Delta.Īnother application of the six-lead motor, used in the U.S. This allows Europe to take advantage of the 1.732 voltage relationship between the Wye and Delta connections (discussed in Part 1) and use them for dual voltage. In the U.S., the ratio of high and low voltage is 2:1 (460 volts:230 volts), but in Europe, it is √3:1 (380 volts:220 volts). Often, the connection will depend on the manufacturing process. Why are single- and dual-voltage motors wound as either Wye or Delta? Why not just standardize on one or the other? Although the Wye and Delta connection diagrams are quite simple, the actual motor windings are far more complex. What is the purpose of these two connections, and why are motors wound as Wye, Delta or a combination of the two? The Wye/Delta combination provides a couple advantages, and we will address them in this column. We will take a detailed look at each of these a little later. The twelve-lead motor will accommodate a combination of dual-voltage and a Wye/Delta connection. These lead combinations are designed to accommodate single or dual voltages and Wye, Delta or Wye/Delta winding connections. Note that these numbers are all multiples of three since their combinations must accommodate three incoming phases. The most common numbers are three, six, nine or twelve. You have probably noticed that three-phase motors can have a varying number of leads exiting the junction box.
